We have all become more aware of the impact of plastic waste on our environment. The BBC programme ’Blue Planet II’ and others have had a profound effect on public perception. The idea that plastic is disposable is no longer acceptable. However scientific research had been a largely ignored consumer of single-use plastics. This is no longer the case.
Many articles now focus on reducing lab waste and recycling or re-using laboratory plastic:
- Can science break its plastic addiction? This article published by Wellcome was also reproduced in The Guardian [1] and on CNN [2]
- Reduce, reuse, recycle: sustainability in the lab
- How to reduce your lab’s plastic waste from The Biologist
A study from the University of Exeter estimates that laboratories worldwide generate 5.5 million tonnes of plastic waste each year – equal to 83% of the plastic recycled worldwide in 2012. Often the scale of the issue is only fully seen by the technicians who collect lab waste and send it to be ‘autoclaved’ – a process that is itself very energy intensive – and finally to landfill. Without scientific research we wouldn’t have the knowledge, technologies, products and medicines that are vital to 21st-century lives, but there is a growing recognition that we must reduce the associated laboratory waste and make science more sustainable.
At first sight, sample management software or a LIMS system might not be the most obvious tool to help reduce lab waste. However, incremental efficiency savings in every aspect of the management of your sample inventory can add up to a very significant reduction of waste and energy consumption.
This applies not only to plastic waste, but to general reductions in the consumption of labware, reagents, storage and energy – all of which improve laboratory running costs along with reducing lab waste.
1. How tracking sample history helps to minimise lab waste
How long have your samples been in storage? What has happened to them during that time? If you have an accurate record of each sample’s life history, this can be used to produce several efficiencies:
Shelf life: What determines your sample’s shelf life and are you able to track it? Is it a fixed number of months? Or is it based on sample usage? If so, accurate tracking could save little-used samples from being thrown away unnecessarily.
Sample usage: if samples are no longer used because a project has closed down or their owner has left the company, perhaps they could be more efficiently stored in a central repository that does not need frequent access? Alternatively, tracking them down and disposing of them frees up storage space and avoids the need to run additional freezers.
Freeze/thaw cycles: The quality of small molecule solution stock is affected by repeated thawing and re-freezing. An alternative to annually restocking all samples, is to count thaw/freeze cycles and replace those samples at highest risk.
The benefits of tracking these three indicators are:
- Reduces the need to refresh certain samples, saving on labware and researcher time
- Indicates when a sample needs to be refreshed sooner, which avoids wasting downstream labware and assay reagents producing inaccurate data
Sample management software or LIMS, such as Titian’s Mosaic, is designed to track the entire lifecycle of a sample from creation to disposal and automatically note the number of times a sample has been through a freeze/thaw cycle. It is then easy to run reports of what has been done in the lab to identify the savings listed above.
Mosaic software has close integrations with lab automation that can be used to identify and remove out of date samples. For example, information on samples’ DMSO percentage from a Beckman Coulter Echo® can be tracked and reported on through the Mosaic software interface. Degraded samples can be flagged for removal as soon as they pass a certain threshold.
2. Minimise waste by using materials efficiently
Running assays using full plates uses reagents and plates most efficiently, but individual researchers won’t necessarily need to use a full plate of compounds for each assay.
Researchers can use sample management software to request assays to be run on their chosen samples. Mosaic software has an Assay Requesting Module which gives an overview on which assays are going to run and when. Multiple orders for the same assay are consolidated in the assay queue. The Sample Management operator can choose the number of samples to process to fulfil the assay(s) most efficiently – perhaps opting to leave some samples to be added to the next assay run.
The inventory of a sample management or LIMS system is easily searchable by many different criteria. This allows groups or departments to share reagents rather than ordering and maintaining separate stocks of the same thing. This is particularly useful for items that only get used occasionally, especially where they have a limited shelf life. As well as reducing reagent costs, it also reduces the number of containers that need to be cleaned, recycled or sent to waste.
Pipetting of liquids – whether manual or automated – usually generates high levels of consumable waste as tips tend to be single-use to avoid cross-contamination. However, there are three ways your lab can reduce this:
- Tip reuse: if you are just dispensing system fluid or DMSO, do you need to change pipette tips? Tip use can often be set when programming your liquid handler, allowing you to reduce plastic use. Integrated sample management software like Mosaic will let you specify when to change tips as part of creating the sample processing workflow, without needing to program each instrument individually.
- Tipless dispensing: acoustic dispensers do not require pipette tips, removing one element of waste. Mosaic software offers off-the-shelf close integration with Beckman Coulter Echo and Access® platforms, and AcoustiX® Tubes, to help you manage acoustic liquid handling easily.
- Miniaturised dispensing: Using nanolitre volumes in assays cuts down on the amount of plastic required for the pipettes, allows assays to be concentrated into a smaller number of high density plates and conserves sample so it goes further. Acoustic dispensers combine the benefits of both miniaturised volumes and tipless dispensing.
Learn more about Mosaic FreezerManagement and the benefits it brings in our demo video - watch it here.
3. Make savings from efficient freezer storage management
In an earlier blog, we asked “How much does it cost to run my laboratory freezer?”
In summary, one standard -80°C laboratory freezer consumes around 6900 kWh of electricity each year. In countries where energy prices are high, this means that approximately €1600/ $1700 / £1400 are spent each year for each freezer on electricity alone. Where fossil fuels are used to generate a significant proportion of the electricity used, calculations on the amount of carbon dioxide produced per kWh show that 6900 kWh produces between 2000-5000 kgs of CO2, or the equivalent of driving an average car 11,500 miles. And this is before you consider the associated energy requirements of the building housing the freezers, which may require energy-intensive air-conditioning.
Clearly then, it is essential to make the most efficient use of freezer space to maximise what can be stored in each one, and to minimise the numbers of freezers required.
Mosaic FreezerManagement can help you do this. It is simple and affordable software that tracks your entire storage inventory to optimise freezer use and also:
- Guides the operator or scientist to the exact sample location, thus ensuring freezer doors are open for the minimum amount of time, which conserves energy and sample integrity
- Records sample properties, ensuring different samples are kept at the correct temperature for that sample type
- Includes a search function to avoid redundant purchases of reagents or other materials
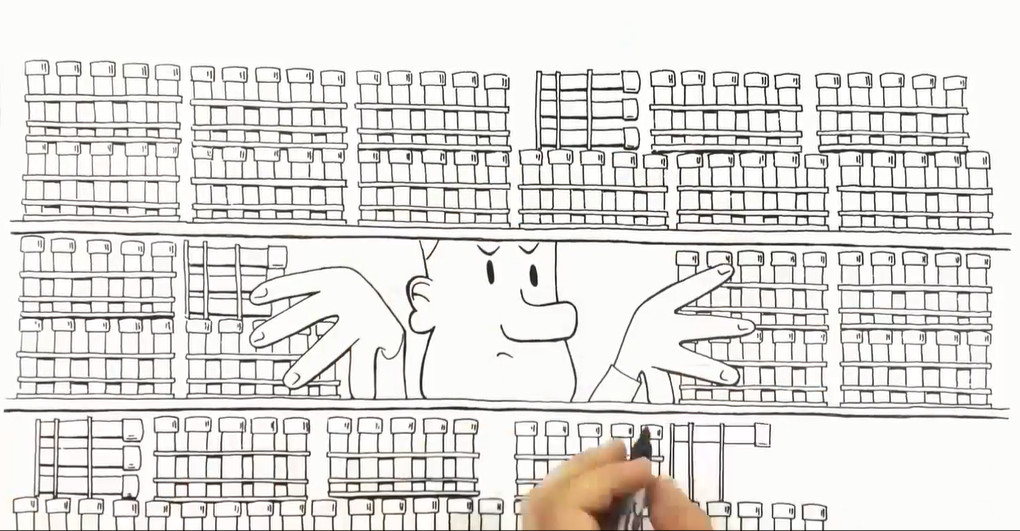
4. What about reuse and recycling?
Finally, returning to a theme in the referenced articles above, not all lab plastics are too contaminated to be recycled. An example of this was highlighted by the Francis Crick Institute (FCI), involving glucose in plastic media bottles. Glucose (sugar) itself is non-hazardous, but recycling companies are generally wary of scientific jargon on labels. By finding contractors with the right expertise the FCI now recycle their media bottles after initial washing.
Recycling companies cannot normally deal with mixed materials, so you may need to review your choice of labware to ensure it is recyclable. For example, to ensure a tube cap and body are made of the same materials. Alternatively, it may mean swapping some items for reusable glass which can be washed.
Good inventory software also helps this process, as it tracks labware types and provides essential reports on usage. This allows you to assess the most and least commonly used items in your lab. Perhaps reducing the variety of labware types, or changing the materials of some, could result in big waste savings for your lab?
Consider the bigger picture when reducing waste
An effective sample management software or LIMS system, has an essential role to play in identifying areas of lab waste and efficiency savings in every aspect of the management of your sample inventory. These savings apply not only to plastic waste, but to general reductions in the consumption of labware, reagents, storage and energy – all of which improve your lab running costs as well as reducing laboratory waste.
Read our essential guide to managing laboratory samples:
This white paper reviews the challenges and best practice for managing samples in your lab, and discusses where sample management software, such as Titian’s Mosaic, can bring you savings.
REFERENCES
[1] The Guardian - Can laboratories curb their addiction to plastic?
[2] CNN – Can science break its plastic addiction?